Principles of facility layout in production management
Principle of minimum movement or travel
Many manufacturing companies determine the minimum distance needed to travel or move while manufacturing the products. It consists of the distance between two workstations, two departments, or the place where specific operations are executed.
Minimum travel or movement of workers and/or materials reduces the time and cost required to complete operations. Time study and method study or work measurement determines the standard time within which the operations need to complete. Method study determines the effective and convenient way that is the standard way of completing the task or operations.
Example 01:
In the steel manufacturing plant, facility layout can reduce the distance between the place of storage and place of manufacturing by the effective structure of arranging all the physical facilities.
Example 02:
Reduced distance between the place of the canteen and the place of workstation reduces the time required to take the tea break and launch break. Employees can start work more quickly after the break.
Example 03:
The availability of raw material stock near manufacturing places can increase the productivity of the organization. facility layout can make such arrangements. Poor facility layout may responsible for reducing the convenience of making available the required material for manufacturing quickly.
Principle of space usage
Most manufacturing organizations face limitations of space available for setting up manufacturing facilities. Complete and proper use of all the available space is an imperative necessity of any manufacturing plant. The structure of arranging all the physical facilities makes optimum utilization of available space.
Proper location of machinery, storage, administration, and many other departments of the manufacturing plant is the basic requirement. Facility layout provides the proper structure for locating all the physical facilities properly.
Example 01:
Car manufacturing companies or vehicle manufacturing companies require maximum space for the storage of their material and completed vehicles. It becomes very difficult to maintain the stock if demand is more. The inventory management department strives to reduce the waiting time by making available all the materials and products. facility layout can make the provision of required space for storage of material as well as produced vehicles.
There is always a difference between available space and required space for manufacturing organizations. because the organization always strives to expand its production capacity.
Principle of Unidirectional flow
Operations executed and material moved in the manufacturing department should be in the forwarding direction. Repetitive execution of the same operations due to mistakes increases the cost and time spend. Facility layout can reduce the time required to execute the operations along with the time required to move the material. The long distances between two workstations and operations engage more time and cost.
Example 01:
Batch production makes the provision of executing all the similar operations at the same place. Paint and chemical companies utilize process or functional layouts for excellence in the execution of their operations.
Example 02:
LED TV manufacturing companies adopt the product or line layout to manufacture the products in mass quantity. Facility layout with the product or line production enhances productivity and reduces cost and time.
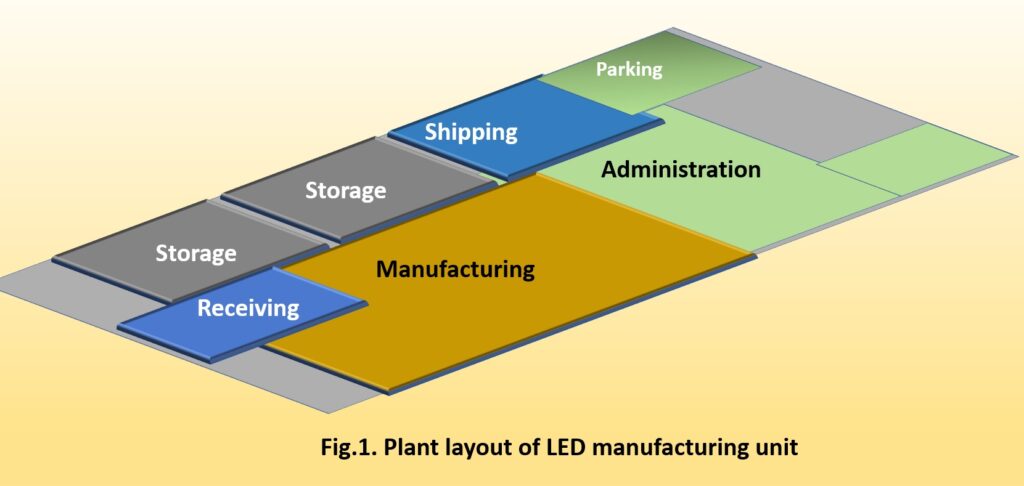
Principles of job satisfaction
All the employees involved in completing the operations of manufacturing need easiness and convenience. The facility layout makes provision for a simplified work environment. A complicated work environment reduces the job satisfaction of Workers and other employees. Facility layout can enhance job satisfaction by increasing the easiness of working.
Example 01:
Every employee expects a healthy work environment. It is possible through better facilities such as canteen, work area given, sick room, parking area, etc. such facilities may satisfy the employees when provided with better facility layout.
Principles of minimum investment in fixed capital
Excellent Facility layout can avoid the requirements of unnecessary machines and other physical facilities. The cost of manufacturing requires maximum capital for any manufacturing organization. precise facility layout can reduce the overall investment in fixed capital by making optimum utilization of available and fewer resources.
Example 01:
Automobile companies require more space and heavy machinery for manufacturing. Better facility layout directs the use of required machinery, equipment, and instruments. It avoids unnecessary investments which are easy to avoid by improved layout. Unnecessary investments in the excess parking area, storage place, and maximum travel or movement between two places within the organization. Machinery and building are the major investment area for any manufacturing company.
Principles of integrated and compactness
Integrated work and compactness in the overall execution make the excellency in the execution of all the operations. The manufacturing system always strives to execute effectively, conveniently, and properly. Facility layout makes the provision of a compact system which enhances the connectivity of all the workstations easily.
Principles of maximum visibility and minimum handling
Visibility is an essential factor in all manufacturing organizations. less visibility increases the requirements for power consumption. Facility layout direction the plant building to make the provision of proper ventilation and light.
Material handling is done in the manufacturing organization to move the material from one place to another. It is done by industrial trucks or by other machinery. The long-distance between the place of storage and the place of manufacturing causes to spend more time and cost. Facility layout can prepare a structure of all the physical facilities located at small distances
Principle of the safety of employees
Every employee needs their safety while working with machinery and complicated equipment. All the chemical industries, electrical industries, and some heavy machinery manufacturing companies consist of several operations that involve high risk. Chances of accidents are more in such operations. The company should consider the employee’s safety while preparing the facility layout.
Principles of flexibility
Most manufacturing companies are interested in the expansion of their physical facilities. Sometimes they need advancements in technology for manufacturing. Facility layout should provide easiness while making upgradation in the physical facilities. It can increase the production capacity of an organization and accuracy too.
Conclusion
Manufacturing companies adopt different types of layouts as per their requirement. Types of products and the company’s objective determine the selection of layout. Such as process or functional layout used when similar operations are executed at the same place. Production layout utilized for mass production. Facility layout can make the provision excellency in the execution of all the operations according to the types of layouts. Type of layout is selected by manufacturing organization according to the suitable production type production type
Lenovo IdeaPad Slim 5 Intel Core i5
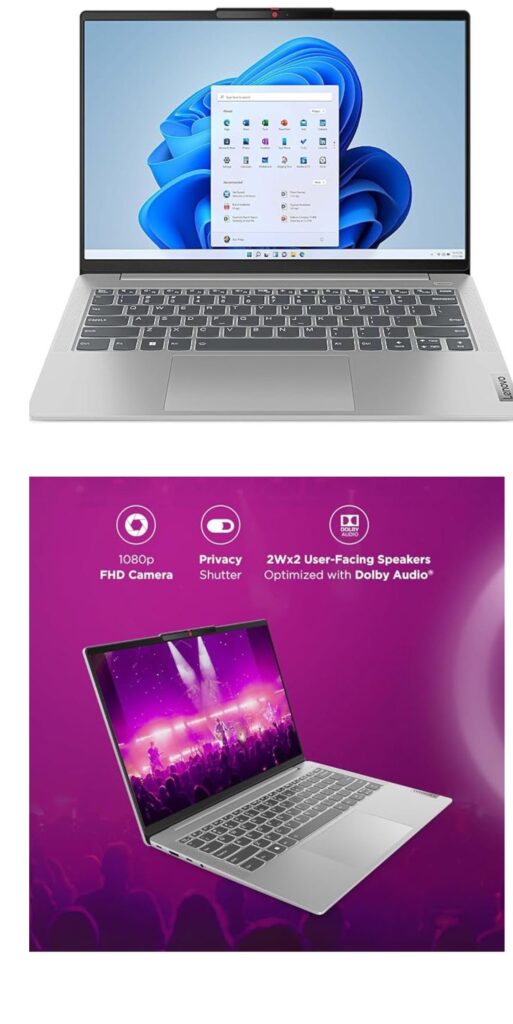